VVT observations - current vs. advance
#82

I'm in the midst of finalizing mine. I know I've said that a number of times, but I'm convinced I'm in the home strech. I'll have the car on the dyno next week for a final run-up and see where it gets me. The two days after that, I'll be competing in the Dixie National Tour with the car.
I have ~1000 miles on the controller now, however, the code has changed significantly over that time. The overall operation has become more efficient, though the concept and operability as a whole has remained largely unchanged.
The controller will be lower in price than your typical MS-1 board.
I have ~1000 miles on the controller now, however, the code has changed significantly over that time. The overall operation has become more efficient, though the concept and operability as a whole has remained largely unchanged.
The controller will be lower in price than your typical MS-1 board.
#88

Out of curiousity I opened up the VVT actuator.
There is a locking pin that pops in place at full retard when there is no oil pressure. Once this pin is pushed in the actuator is free to advance. There is a partial detent at around 12* advance (crank degrees) where without oil pressure it takes a bit of extra effort to get it to advance beyond that. That is, if the piston is pushed in, it will freely advance from 0 to 12*. Once you pop past that 12* point it is free to advance further. I'm not sure if more oil pressure would push the piston so that this detent goes away. I'm not sure if this affects the dynamics of the system, though I vaguely remember in my in-car-stock-ECU testing that there seemed to be an amount of advance it would stay in, which was around 12* IIRC, when it wasn't at full retard.
The surface area against which oil pressure acts to advance or retard is
14.5 mm x 23 mm x 4
with a moment arm of 28 mm. So oil pressure * all of them = torque.
Remember that the spool valve diverts oil continuously between the advance and retard chambers depending on current / duty cycle.
More later. I have pix and vids.
There is a locking pin that pops in place at full retard when there is no oil pressure. Once this pin is pushed in the actuator is free to advance. There is a partial detent at around 12* advance (crank degrees) where without oil pressure it takes a bit of extra effort to get it to advance beyond that. That is, if the piston is pushed in, it will freely advance from 0 to 12*. Once you pop past that 12* point it is free to advance further. I'm not sure if more oil pressure would push the piston so that this detent goes away. I'm not sure if this affects the dynamics of the system, though I vaguely remember in my in-car-stock-ECU testing that there seemed to be an amount of advance it would stay in, which was around 12* IIRC, when it wasn't at full retard.
The surface area against which oil pressure acts to advance or retard is
14.5 mm x 23 mm x 4
with a moment arm of 28 mm. So oil pressure * all of them = torque.
Remember that the spool valve diverts oil continuously between the advance and retard chambers depending on current / duty cycle.
More later. I have pix and vids.
#95

The dyno session went well and the results were as expected. There was no discernible power loss or gain. We were able to pick up a couple HP here and there with some tweaks but I think we pretty much nailed it the first time (which was last August). In the process, I did find some noise on the map signal and will have to filter that out. Furthermore, that pesky initial overshoot that I've been chasing is still there, but it's just a matter of playing with values to get it smoothed.
After the dyno, the car made a 4 hour trip to the SCCA Dixie National Tour without issue. It drove quite nicely I might add. The event wasn't bad, but the driver showed that he needs a lot of work as I finished 6/15 being only 0.12 seconds out of the trophies.
The following is the short list of things to do:
-Re-work the power supply to make it more automotive (and user) friendly.
-Add filtering on the MAP signal
-Tighten up the PID algorithm
-Chase down some communication quirks
Below is an image of a log I took while on the dyno. FYI, each sample on the x-axis is recorded roughly every 40mS. There is an odd anomaly where the target increases, as does the advance, but it never meets the target (on the later half of the plateau). I've never seen this until running the dyno. I'm beginning to seriously question the implementation of a strictly linear PID implementation and wonder if it should be more focused around the "hold" position of the OCV that Jason has previously discussed.
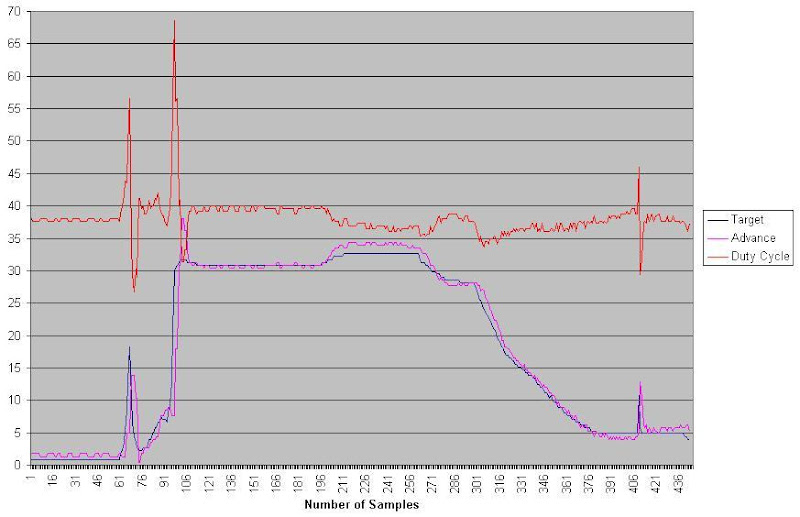
I apologize this is taking so long and I know you guys are anxious, but I don't want to release something that doesn't work at 100%. I want this to be done just as much as the next guy. I will say that it's very close!
I'll keep the updates coming.
After the dyno, the car made a 4 hour trip to the SCCA Dixie National Tour without issue. It drove quite nicely I might add. The event wasn't bad, but the driver showed that he needs a lot of work as I finished 6/15 being only 0.12 seconds out of the trophies.
The following is the short list of things to do:
-Re-work the power supply to make it more automotive (and user) friendly.
-Add filtering on the MAP signal
-Tighten up the PID algorithm
-Chase down some communication quirks
Below is an image of a log I took while on the dyno. FYI, each sample on the x-axis is recorded roughly every 40mS. There is an odd anomaly where the target increases, as does the advance, but it never meets the target (on the later half of the plateau). I've never seen this until running the dyno. I'm beginning to seriously question the implementation of a strictly linear PID implementation and wonder if it should be more focused around the "hold" position of the OCV that Jason has previously discussed.
I apologize this is taking so long and I know you guys are anxious, but I don't want to release something that doesn't work at 100%. I want this to be done just as much as the next guy. I will say that it's very close!

#98

If it never accelerated when the peak was passed, we could forgo belt tensions. :-)
That is pretty interesting. I'm assuming you already did the multiply-by-4 thing, right?
Somehow, I envision the drains being pretty small, and really it's the viscosity keeping it from going anywhere. The valve in the middle is... using the incompressibility of the oil to provide the force to get past the cams. Would you say the pressure in your shock absorbers, being, oh... sometimes 40 psig... is enough to keep your car from slamming to the ground on the first bump, acting only on a piston 1 sq in in frontal area? Certainly there's not a thousand pounds there but it does keep the car from moving. The 10 ft-lbs is for advancing, I'm thinking the pressure differential is almost always 0.
That is pretty interesting. I'm assuming you already did the multiply-by-4 thing, right?
Somehow, I envision the drains being pretty small, and really it's the viscosity keeping it from going anywhere. The valve in the middle is... using the incompressibility of the oil to provide the force to get past the cams. Would you say the pressure in your shock absorbers, being, oh... sometimes 40 psig... is enough to keep your car from slamming to the ground on the first bump, acting only on a piston 1 sq in in frontal area? Certainly there's not a thousand pounds there but it does keep the car from moving. The 10 ft-lbs is for advancing, I'm thinking the pressure differential is almost always 0.
#99

Jason, do you have a VVT gear actuator lying around that you might be able to disassemble and measure the surface area of the faces of the [three] vanes? With this in hand, we can determine how much force is applied to the actuator via various oil pressures.
Using arbitrary numbers, if each face is 1 square inch, the oil pressure at say 60 PSI would provide 180 pounds of force to advance the camshaft relative to the gear's position. This is with the OCV hypothetically wide open, of course.
Using arbitrary numbers, if each face is 1 square inch, the oil pressure at say 60 PSI would provide 180 pounds of force to advance the camshaft relative to the gear's position. This is with the OCV hypothetically wide open, of course.