Oil distribution and sensor location idea
#1
Thread Starter
Junior Member
iTrader: (4)
Joined: Dec 2007
Posts: 363
Total Cats: 0
From: Springfield, Mass

I've read several posts and ways to mount sensors and feed lines for the turbo but I didn't like the idea of drilling and tapping holes into my engine. So I did some thinking and kinda came up with an idea.
Objective:
To supply oil to turbo and a central location for my sensors, stock oil press. aftermarket oil press. and temp sensors. I would like the sensors all in the same place for ease of installation and access.
Idea:
Begi oil feed fitting at the block running to a distribution block with several 1/8npt fittings. Attach the sensors to the various ports and have a line running from the distribution block to the turbo. I found a vacuum block with ports on ebay for 20$.
http://cgi.ebay.com/ebaymotors/ws/eB...K%3AMEWAX%3AIT
I would mount the distribution block to the firewall.
What do you think? I'm open to any suggestions.
Objective:
To supply oil to turbo and a central location for my sensors, stock oil press. aftermarket oil press. and temp sensors. I would like the sensors all in the same place for ease of installation and access.
Idea:
Begi oil feed fitting at the block running to a distribution block with several 1/8npt fittings. Attach the sensors to the various ports and have a line running from the distribution block to the turbo. I found a vacuum block with ports on ebay for 20$.
http://cgi.ebay.com/ebaymotors/ws/eB...K%3AMEWAX%3AIT
I would mount the distribution block to the firewall.
What do you think? I'm open to any suggestions.
#4
Joined: Sep 2005
Posts: 33,556
Total Cats: 6,933
From: Chicago. (The less-murder part.)

For feeding a turbo and one or more pressure sensors, this sounds like a fine idea.
Might be problematic for oil temp- those sensors tend to be fairly long, though you might be able to stick it in sideways. It's likely that a temp sensor will read low, owing to the fact that there's going to be relatively little flow through the block, and fairly significant radiant dissipation of heat from the block.
Alex- he's running a '96 engine, which doesn't have the hotside feed that the earlier blocks did. So, essentially, he is using the one preexisting port which he has.
Scotty- not sure where you'd drill & tap for this. I examined the casting on the back of an NB block, and it looks like you'd have to remove and tear down the block and then drill a 1/8" wide hold 6" deep, perfectly straight, which is a little outside the capabilities of most people.
Might be problematic for oil temp- those sensors tend to be fairly long, though you might be able to stick it in sideways. It's likely that a temp sensor will read low, owing to the fact that there's going to be relatively little flow through the block, and fairly significant radiant dissipation of heat from the block.
Alex- he's running a '96 engine, which doesn't have the hotside feed that the earlier blocks did. So, essentially, he is using the one preexisting port which he has.
Scotty- not sure where you'd drill & tap for this. I examined the casting on the back of an NB block, and it looks like you'd have to remove and tear down the block and then drill a 1/8" wide hold 6" deep, perfectly straight, which is a little outside the capabilities of most people.
#6
Joined: Sep 2005
Posts: 33,556
Total Cats: 6,933
From: Chicago. (The less-murder part.)

I actually kind of like it, to be honest. Not for a temp sensor, but for distribution of oil to the pressure sensors and turbo. Much better, IMO, than hanging the weight of an oil pressure sensor off the end of a Tee fitting screwed into the side of the block.
#7
Thread Starter
Junior Member
iTrader: (4)
Joined: Dec 2007
Posts: 363
Total Cats: 0
From: Springfield, Mass

Thanks for the replies and suggestions. I will probably pull the trigger on this setup and post up once I have it done with findings.
Thanks for the info on the readings of the temp sensor, maybe i'll just have to use one of the those oil drain senders.
Thanks for the info on the readings of the temp sensor, maybe i'll just have to use one of the those oil drain senders.
#10

That's basically what I ended up doing. Routed a line off the OPG feed, that line fed both the turbo and the new OPG. Didn't need a whole oil mani, just a tee.
Was very confused about block drilling. Thought everyone used the OPG port on late blocks and the hot side port on early ones.
--Alex
Was very confused about block drilling. Thought everyone used the OPG port on late blocks and the hot side port on early ones.
--Alex
#11
Joined: Sep 2005
Posts: 33,556
Total Cats: 6,933
From: Chicago. (The less-murder part.)

[QUOTE=AlexO35;668402]That's basically what I ended up doing. Routed a line off the OPG feed, that line fed both the turbo and the new OPG. Didn't need a whole oil mani, just a tee.[quote]This is what I've seen most folks do, as well. There has, however, been some concern about whether a tee (or the BSP adapter fitting its screwed into) will crack or break if it has a large and heavy oil pressure sensor (either OEM '90-'94 or aftermarket) hanging off the end of it. Remoting the assembly to a manifold (or simply remoting the tee) alleviates this concern.
I think that perhaps Scotty was suggesting that a person drill out a late-model block to create the same coldside feed as the early blocks.
I looked at doing this late last year. The casting certainly would support it, however actually drilling the hole would be tenuous. Here's what it looks like on the back of an NB block:

Basically, where that horizontal line is that says "feed to turbo" is where you'd need to run a drill of appx 1/8" diameter through about six inches of solid iron, remaining perfectly centered and without deviating by so much as a degree in any direction.
You could much more easily put a hole into the block on the hot side to reach the main galley, but I don't see how this would be advantageous vs. using the OPG hole. You still have to cross over the engine bay with the line. Well, it'd save you a tee, I suppose.
Hmm. Now that I think about it, I might just do this on my '99 block...
Was very confused about block drilling. Thought everyone used the OPG port on late blocks and the hot side port on early ones.
I looked at doing this late last year. The casting certainly would support it, however actually drilling the hole would be tenuous. Here's what it looks like on the back of an NB block:

Basically, where that horizontal line is that says "feed to turbo" is where you'd need to run a drill of appx 1/8" diameter through about six inches of solid iron, remaining perfectly centered and without deviating by so much as a degree in any direction.
You could much more easily put a hole into the block on the hot side to reach the main galley, but I don't see how this would be advantageous vs. using the OPG hole. You still have to cross over the engine bay with the line. Well, it'd save you a tee, I suppose.
Hmm. Now that I think about it, I might just do this on my '99 block...

#15
Thread Starter
Junior Member
iTrader: (4)
Joined: Dec 2007
Posts: 363
Total Cats: 0
From: Springfield, Mass

Aluminum distribution part came in today and I think this will work great. It's a little bigger than I imagined but will be great for my plans.
It looks like there will be plenty of room for flow even with the temp sensor.
[IMG]
[/IMG][IMG]
[/IMG]
I plan on feeding the oil in through the 90* fitting on the bottom and then out the top to the turbo. I just have some stuff in the ports to make sure they all are 1/8NPT.
[IMG]
[/IMG]
It looks like there will be plenty of room for flow even with the temp sensor.
[IMG]
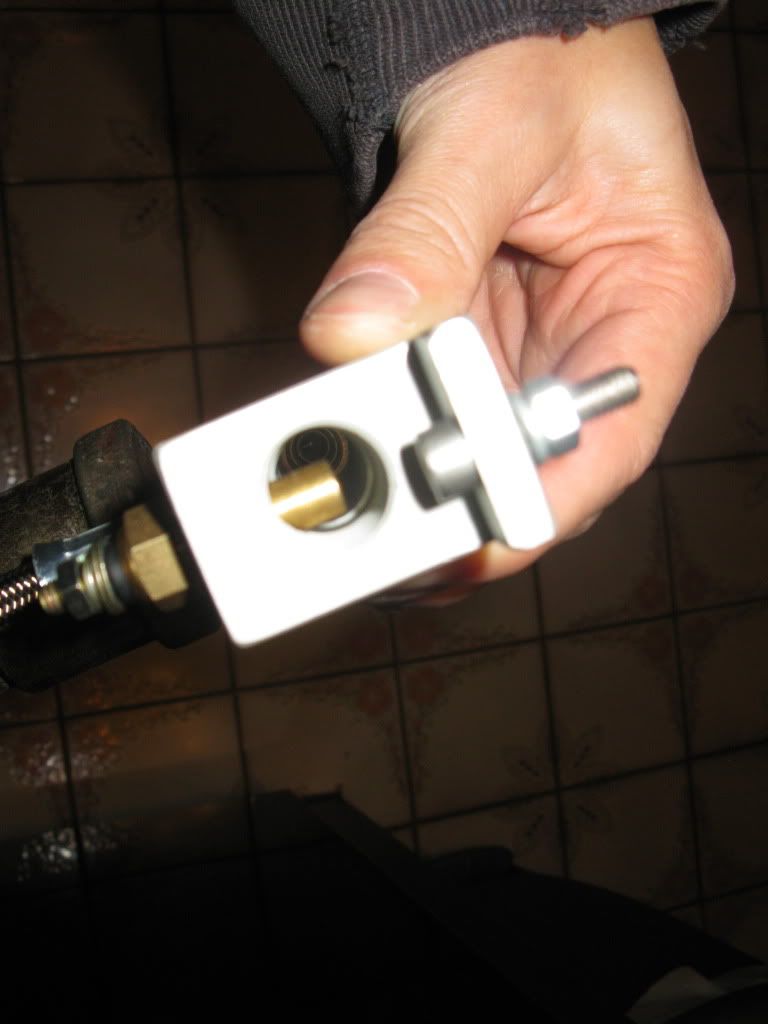
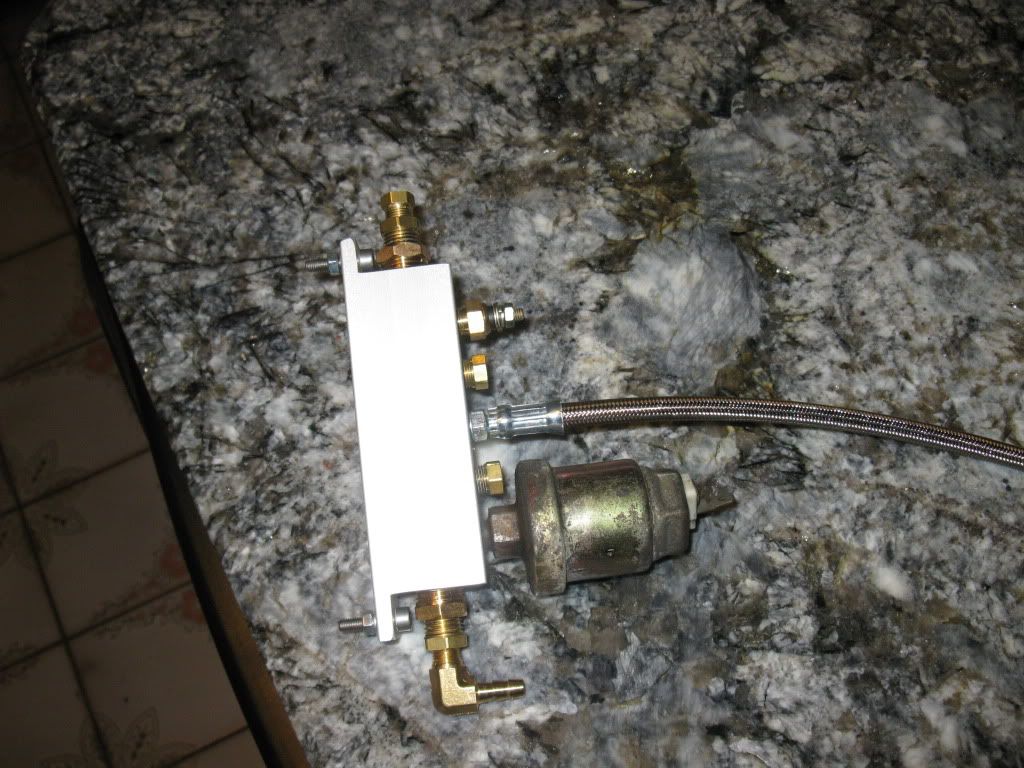
I plan on feeding the oil in through the 90* fitting on the bottom and then out the top to the turbo. I just have some stuff in the ports to make sure they all are 1/8NPT.
[IMG]
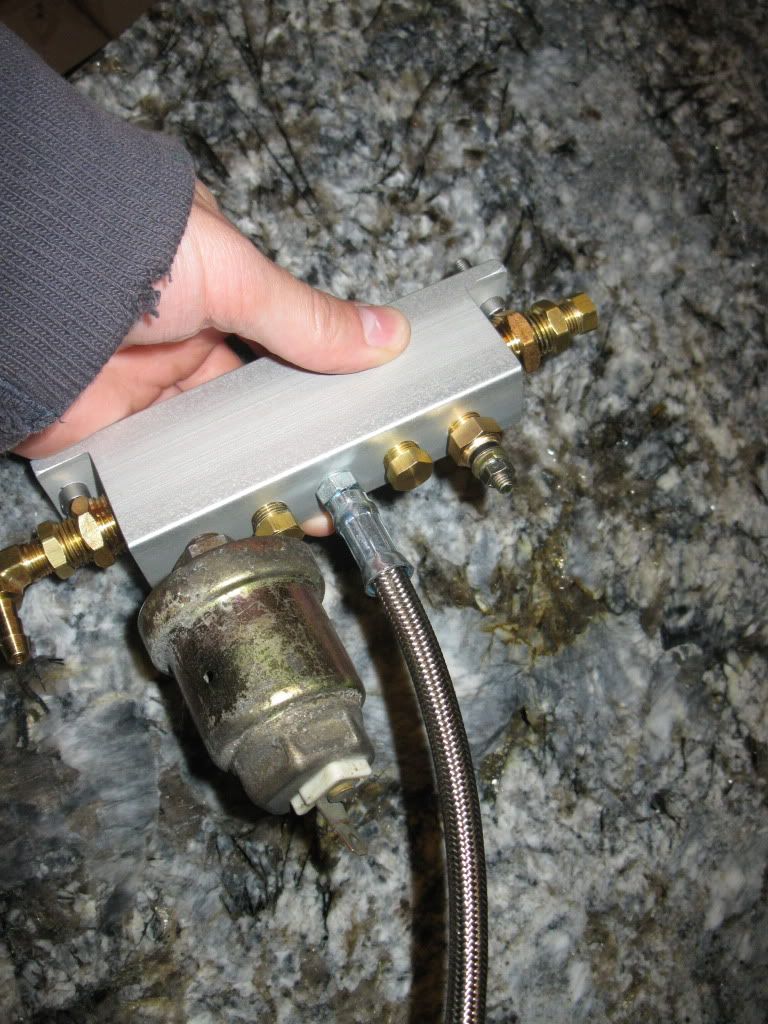
#16

Personally, I don't think I'd use a hose barb anywhere in that setup. It's just asking for leaks, and you want to maintain as much pressure as possible throughout. And be sure you use plenty of thread sealer. I had one of those that leaked vac like crazy no matter what I did. I eventually just pitched it because I could never make it seal properly.
#17

Make sure you use a little Teflon lube to help seal the threads, not the tape. Just not too much, ask hustler why.
I'm no fluid engineer, but sill you loose pressure to the turbo with that big opening? I'm with baron, I'd use npt-AN fittings on the end, not hose barbs.
It looks like a sound idea, hope it works.
Edit: if you're smart, those Npt-AN fittings should get rid of one of this adapters. They're needless potential leak points.
I'm no fluid engineer, but sill you loose pressure to the turbo with that big opening? I'm with baron, I'd use npt-AN fittings on the end, not hose barbs.
It looks like a sound idea, hope it works.
Edit: if you're smart, those Npt-AN fittings should get rid of one of this adapters. They're needless potential leak points.